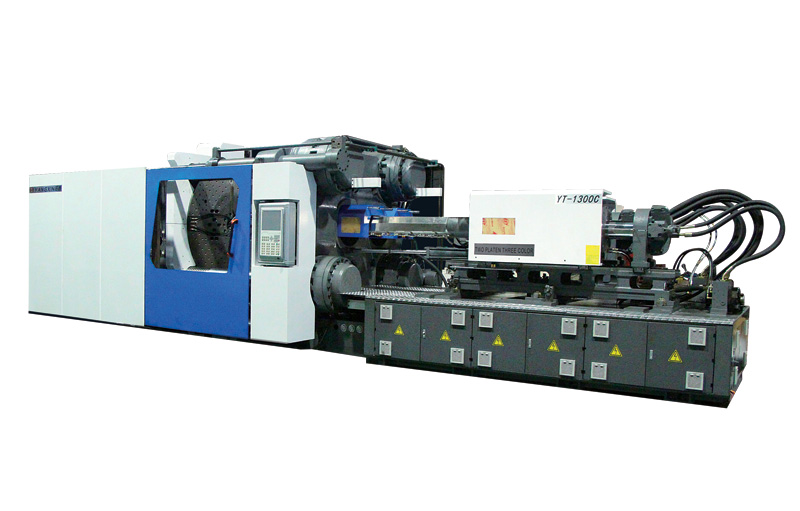
Three-plate three-color molding machine
Model number: YT-1300T
Views:
Support hotline:86-752-6833832
Detailed description
Precise locking system, outstanding efficiency, efficient servo drive, all meet all requirements. Focus on customer products, provide a complete set of technical solutions for customers, and create better investment returns and customer experience for global customers.
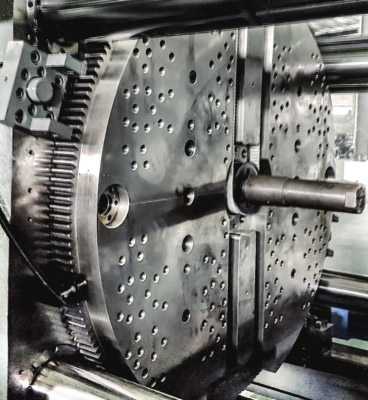
A rotary axis is located at the center of moveable platen, which could drive mould move around to produce individual two-component products.
There are two independent barrel sets at injection unit; each of them could do unit injection action simultaneously.
According to the request of products, the machine with flexibility could do ejection then tum the rotary table or turn rotary table firtst then do the ejection actian as well.
This series machine is suitable for producting keyboard, handle bar. and hanger.....and etc.
It is suitable for many different applications, and has many technical functions, which will bring you more efficient production.
Equipped with six stages injection, three stages holding pressure, twostages suck abck and the holding pressure posittion switching controls etc, can flexibly adust according to different products. Precise injectionend and holding pressure position switching practice high precision andhigh stability injection function adopt lindal electrical ruler, precisionreaches 0.01mm, which can accurately control injection strok. it canrecord and display simultaneously samping temperature curve during continuous production process, injection and holding pressure switchingpoint and holding pressure finishing point. Having the function of historical curve allocation, its precision can reach 0.1mm and sytem stability is visiblesix PID stages barrel temperature control is precision can reach. It also has temperature abnormal & electrical wire disconnection alarmeunction, which is able to control the barrel temp-erature accurately. Screwlow temperature staring protection (cold start) can be prevent screw from damage accidentally, adjustable pre-heat temperature keeping and barrel auto heating function, which can arbitrarily set cleaning.
The locking device which is added on both sides of the Rotary Table can prevent effctively the incline of the Rotary Table
Unique and accurate positioning device of the Rotary table cna ensure the stability of mold clamping and prevent mold damage.
The unique reinforced design of Tie Bar and Toggle can effctively absorb the shear stress that generated by mold Clamping to extend the service ilfe of the machine.
Ejector with multi-function on vibration ejection, ejection locate, multiple ejection. Pressure and speed of ejection canset by compuer.
Low pressure result is perfect by equipped with high precision of the low pressure mold closing protection. That can be ste directly by monitor.
Toggle is used by auto lubrication system, lubriction setting can be operated and monitored on the panel directly. And it owns itself lubrication failure alarm.
Adopts MIRLE microcomputer controller, optional closed loop hydraulic control system, showing extremely stable and accurate performance.
The unique design of our company is that the rotary platen does not touch the mold platen when it rotates to reduce the failure caused by abrasion, and accurate posistioning confirmation is made before mold opening to protect the safey of the mold.
The new generation of toggle clamping structure adopted in this machine, combined wutg bix-type mavable platenl and high-rigidity sand platen structure, has a simple and firm design, and throught finite element analysis of deformation and stress distribution, it has really reached the characteristics of high strength and wear-resisting, which can ensure the forming quality and the life of tie bar.
The machine is equipped with a 32-tit elment high-speed CPU and a system reaction rate as high as 1.20ms, which can effctively improve the sensitivity and stability of the machine.
The two respctive of injcection units adopt the new single-cylinder injection structure, which operates independently of injection and feeding, and can perform multiple compound injection actions
Configure servo motor energy saving system to save energy effctively.
Durable: FEAcubicle type temp template structure desing. Compare with common template strength upgrade more 150%, tem plate less deform, screw strength bigger 20% than traditional machine, long lifetime.
Prexibie: according customer repuirement addition ejector strokeand ejector force.
Fit customer to add opening stroke
Flexble choose injection structure to coordinate customer requirement.
Note: The output of this product parameter is calculated according to the specific gravity of polystyrene of 1.05, assuming an efficiency of 0.88. As the product is continuously researched and improved, the design changes are subject to change without notice.
TWO COMPONENT INJECTION MOLDING MACHINE-ROTARY TABLE
It is suitable for many different applications, and has many technical functions, which will bring you more efficient production.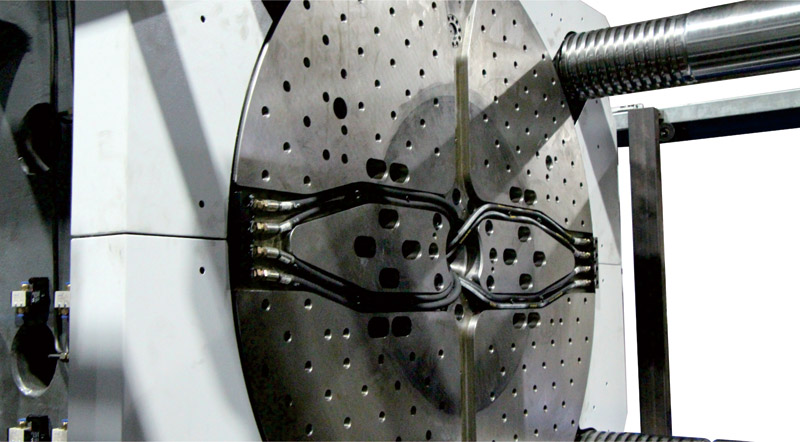
Wide range of applications
High precistion mode change devices and two way 180 degree rotating back and forth, which may put two molds produce two component products.
Precision and stability
Rotation platen with High efficiency gear transmission. High precision Servo Motor-drven. Motor-driven. Fast and smooth, the stop posistion is accurate.Reliable and durable
Self-lubricating wear-resistant surface. During operation, the rotation plate does not come in contact with the platen, thus reducing the possibility of damage caused ty friction.
Diversity choice
Machine comes equipped sith two sets of hydraulic core pulling device on the rotatio platen. Simultaneous water transport device and choose hydraulic, air, and electrical circuit.
Humanized design
The special design, Rotation platen supporting structure effectively prevents the drooping forward of the Rotation platen afer mold installed.
Safe and worry free
With accurate mold positioning holes on platen can ensure precise location for mold installed. 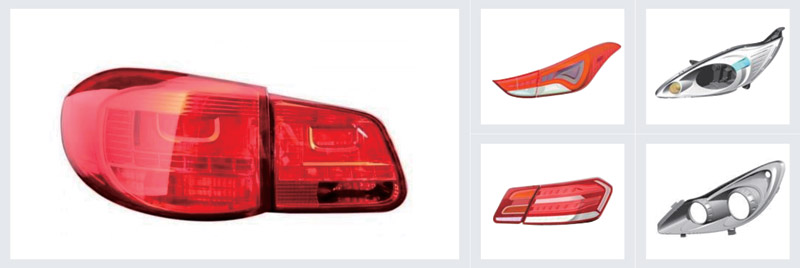
TWO-COLOR INJECTION MOLDING MACHINE-ROTARY AXIS
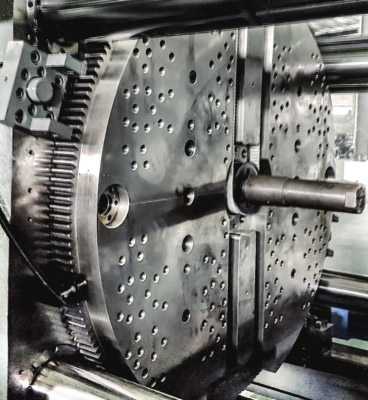
A rotary axis is located at the center of moveable platen, which could drive mould move around to produce individual two-component products.
There are two independent barrel sets at injection unit; each of them could do unit injection action simultaneously.
According to the request of products, the machine with flexibility could do ejection then tum the rotary table or turn rotary table firtst then do the ejection actian as well.
This series machine is suitable for producting keyboard, handle bar. and hanger.....and etc.
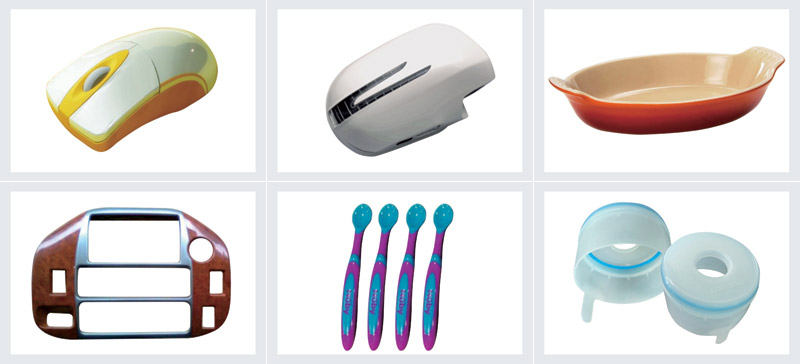
INJECTION UNIT
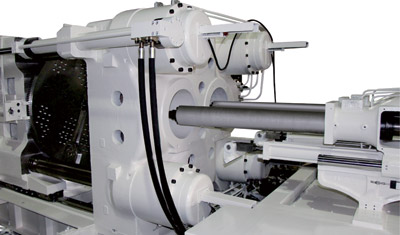
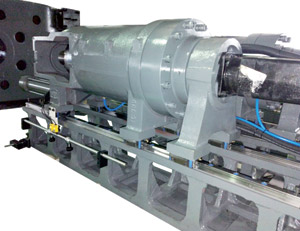
High value
Two isolated barrel sets inject at the same time, thereby reducing cycle time. The shorter cycle time increase productivity of the machine and hence helps to yield bigger profits.
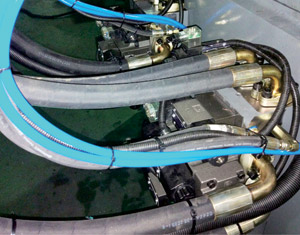
High flexibility
Two sets of indep endent proportion pressure / speed hydraulic circuit control two sets of injection sysetm and ejector system, according to the characteristic of flexible settings to optimize the injection process, to ensure that the production of plastic products of high quality, low-cycle and thus has a stronger market competitiveness.
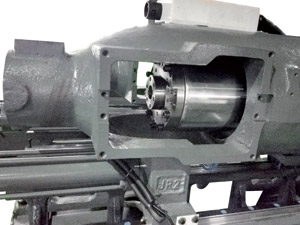
High efficiency
The single-cylinder injection unit with high torque and excellent performandce of hydraulic motor can drive screw directly, reduce iol leak, injection efficiency, high stability.
CONTROL SYSETM:
The controller is adopting 400M high speed CPU, which can equip with semi-closure or fully closed system. Plus personality graphic operation interface, curve online testing function and central network connection management. Ample SPC quality management interface, it is absolutely the best tool to make profit.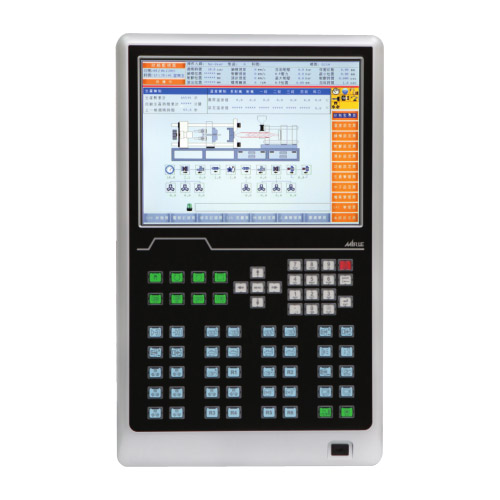
MOLD CLAMPING UNIT
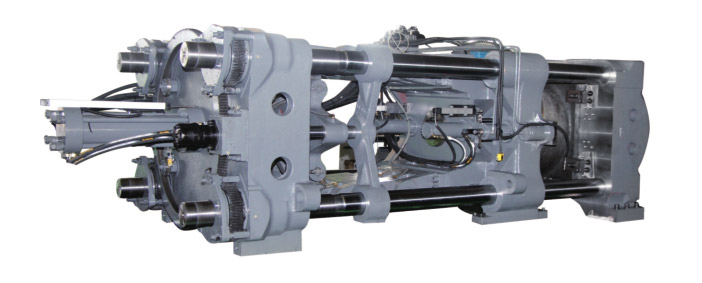
Unique and accurate positioning device of the Rotary table cna ensure the stability of mold clamping and prevent mold damage.
The unique reinforced design of Tie Bar and Toggle can effctively absorb the shear stress that generated by mold Clamping to extend the service ilfe of the machine.
Ejector with multi-function on vibration ejection, ejection locate, multiple ejection. Pressure and speed of ejection canset by compuer.
Low pressure result is perfect by equipped with high precision of the low pressure mold closing protection. That can be ste directly by monitor.
Toggle is used by auto lubrication system, lubriction setting can be operated and monitored on the panel directly. And it owns itself lubrication failure alarm.
TWO COMPONENT INJECTION MOLDING MACHINE-ROTARY TABLE
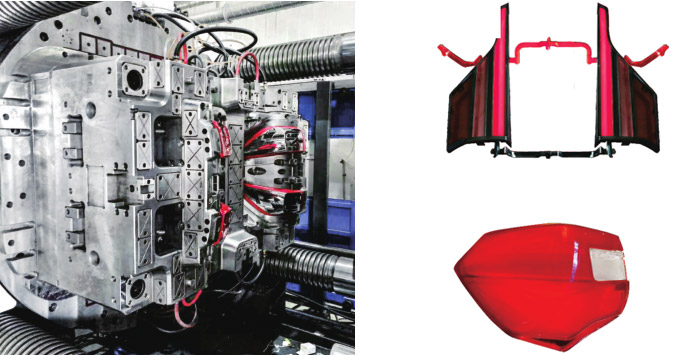
The unique design of our company is that the rotary platen does not touch the mold platen when it rotates to reduce the failure caused by abrasion, and accurate posistioning confirmation is made before mold opening to protect the safey of the mold.
The new generation of toggle clamping structure adopted in this machine, combined wutg bix-type mavable platenl and high-rigidity sand platen structure, has a simple and firm design, and throught finite element analysis of deformation and stress distribution, it has really reached the characteristics of high strength and wear-resisting, which can ensure the forming quality and the life of tie bar.
The machine is equipped with a 32-tit elment high-speed CPU and a system reaction rate as high as 1.20ms, which can effctively improve the sensitivity and stability of the machine.
The two respctive of injcection units adopt the new single-cylinder injection structure, which operates independently of injection and feeding, and can perform multiple compound injection actions
Configure servo motor energy saving system to save energy effctively.
TWO PLATEN DOUBLE COLOR INJE CTION MACHINE
Save space: two platen structure type compare traditional two coior machine, the length shorten 250%-30%Durable: FEAcubicle type temp template structure desing. Compare with common template strength upgrade more 150%, tem plate less deform, screw strength bigger 20% than traditional machine, long lifetime.
Prexibie: according customer repuirement addition ejector strokeand ejector force.
Fit customer to add opening stroke
Flexble choose injection structure to coordinate customer requirement.
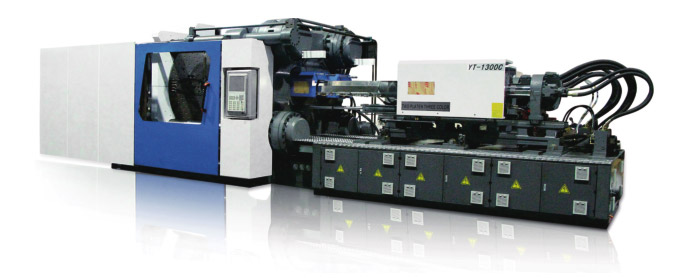
PRODUCTS SPECIFICATION
Project | Unit | YT-450C | YT-700C | YT-1000C | YT-1300C | YT-1600C | YT-1900C | |||||||
Injection Unit | Screw diameter | mm | Φ45 | Φ50 | Φ50 | Φ55 | Φ55 | Φ70 | Φ60 | Φ70 | Φ60 | Φ75 | Φ70 | Φ80 |
Shot volume | cm3 | 397 | 491 | 530 | 641 | 665 | 1462 | 1102 | 1500 | 1102 | 1722 | 1500 | 2286 | |
Shot weight | geam | 367 | 453 | 490 | 592 | 614 | 1351 | 1018 | 1386 | 1018 | 1591 | 1386 | 2112 | |
ozs | 13.0 | 16.0 | 17.3 | 20.9 | 21.7 | 47.6 | 35.9 | 48.9 | 35.9 | 56.1 | 48.9 | 74.5 | ||
Injection pressure | kg/cm2 | 3192 | 2586 | 2803 | 2317 | 2845 | 2210 | 1889 | 2623 | 1889 | 2285 | 2623 | 1815 | |
Injection rate | cm3/sec | 142 | 175 | 162 | 196 | 249 | 403 | 200 | 324 | 246 | 667 | 260 | 353 | |
Clamping Unit | Clamping force | metric tons | 450 | 700 | 1000 | 1300 | 1600 | 1900 | ||||||
Daylight Max | mm | 1400 | 1700 | 1900 | 2800 | 2900 | 3200 | |||||||
Opening stroke | mm | 600-1100 | 700-1350 | 800-1450 | 1000-1600 | 1400-2200 | 1400-2500 | |||||||
Mold thickness | mm | 300-800 | 350-1000 | 450-1100 | 600-1400 | 700-1500 | 700-1800 | |||||||
Rotary Table Diameter | mm | 1250 | 1530 | 1680 | 1930 | 2190 | 2350 | |||||||
Distance Between Barrel Centers | mm | 550 | 650 | 700 | 710 | 710 | 710 | |||||||
Distance between tie bar | mm | 960*830 | 1150*980 | 1260*1050 | 1440*1200 | 1550*1400 | 1760*1520 | |||||||
Ejector stroke | mm | 200 | 200 | 250 | 300 | 300 | 300 | |||||||
Electrical Equipment | Pump Motor power | HP(kw) | 80(60) | 80(60) | 100(74.6) | 120(90) | 130(100.7) | 240(179) | ||||||
Temperature controller | (range)set | 2-(0-400℃)*5 | 2-(0-400℃)*5 | 2-(0-400℃)*5 | 2-(0-400℃)*5 | 2-(0-400℃)*5 | 2-(0-400℃)*5 | |||||||
Heater power | kw | 26 | 25 | 35 | 42 | 60 | 60 | |||||||
Other | Machine dimensions | mm | 6900*2200*2400 | 7300*2400*2500 | 8300*3200*2800 | 9600*3300*2800 | 10400*3500*3100 | 1200*3800*3100 | ||||||
Machine weight | netric ton | 19 | 25 | 35 | 42 | 60 | 95 | |||||||
System pressure | kg/cm2 | 170 | 170 | 170 | 170 | 170 | 170 |
TECHNICAL PARAMETERS
Project | Unit | YC-130 | YC-180 | |||||
Injection Unit | Screw diameter | mm | Φ24 | Φ26 | Φ30 | Φ26 | Φ30 | Φ34 |
Shot volume | cm3 | 55 | 65 | 86 | 77 | 102 | 132 | |
Shot weight | gram | 51 | 60 | 80 | 71 | 95 | 122 | |
ozs | 1.8 | 2.1 | 2.8 | 2.5 | 3.3 | 1.3 | ||
Injection pressure | kg/cm2 | 2406 | 2050 | 1540 | 2547 | 1913 | 1490 | |
Injection Speed | mm/s | 129 | 121 | |||||
Injection Rate | cm3/sec | 58 | 68 | 91 | 64 | 85 | 110 | |
Screw Speed (max) | rpm | 280 | 250 | |||||
Clamping Unit | Clamping force | metric tons | 130 | 180 | ||||
Clamping stroke | mm | 310 | 400 | |||||
Mould Thickness Range | mm | 120-400 | 160-430 | |||||
Rotary Table Diameter | mm | 720 | 830 | |||||
Distance Between Barrel Centers | mm | 350 | 420 | |||||
Distance between tie bar | mm | 600*400 | 710*440 | |||||
Ejector stroke | mm | 70 | 100 | |||||
Electrical Equipment | Pump Motor power | kw | 7.5+7.5 | 9.4+9.4 | ||||
Temperature controller | (range)set | 2-(0-400℃)*5 | 2-(0-400℃)*5 | |||||
Heater power | kw | 7.2 | 8.8 | |||||
Other | Machine dimensions | mm | 5000*1100*1800 | 5584*1600*1840 | ||||
Machine weight | metric tons | 5 | 7 | |||||
System pressure | kg/cm2 | 140 | 140 | |||||
Platen dimensions | ![]() |
![]() |
||||||
Platen dimensions | ![]() |
![]() |
||||||
Platen dimensions | ![]() |
![]() |
TECHNICAL PARAMETERS
Project | Unit | YC-230 | YC-300 | |||||
Injection Unit | Screw diameter | mm | Φ30 | Φ34 | Φ40 | Φ34 | Φ40 | Φ45 |
Shot volume | cm3 | 113 | 145 | 201 | 159 | 220 | 278 | |
Shot weight | gram | 104 | 134 | 186 | 147 | 203 | 257 | |
ozs | 3.7 | 4.7 | 6.5 | 5.2 | 7.2 | 9.1 | ||
Injection pressure | kg/cm2 | 2489 | 1938 | 1400 | 3052 | 2205 | 1742 | |
Injection Speed | mm/s | 106 | 82 | |||||
Injection rate | cm3/sec | 75 | 96 | 133 | 74 | 103 | 130 | |
Screw Speed (max) | rpm | 250 | 250 | |||||
Clamping Unit | Clamping force | metric tons | 230 | 300 | ||||
Clamping stroke | mm | 450 | 500 | |||||
Mold thickness | mm | 180-470 | 195-585 | |||||
Rotary Table Diameter | mm | 960 | 1070 | |||||
Distance Between Barrel Centers | mm | 450 | 500 | |||||
Distance between tie bar | mm | 830*510 | 910*570 | |||||
Ejector stroke | mm | 110 | 110 | |||||
Electrical Equipment | Pump Motor power | kw | 9.4+9.4 | 14.1+14.1 | ||||
Temperature controller | (range)set | 2-(0-400℃)*5 | 2-(0-400℃)*5 | |||||
Heater power | kw | 8.8 | 13 | |||||
Other | Machine dimensions | mm | 6800*1800*2100 | 7000*1900*2200 | ||||
Machine weight | metric tons | 13 | 15 | |||||
System pressure | kg/cm2 | 140 | 140 | |||||
Platen dimensions | ![]() |
![]() |
||||||
Platen dimensions | ![]() |
![]() |
||||||
Platen dimensions | ![]() |
![]() |
TECHNICAL PARAMETERS
Project | Unit | YC-450 | YC-550 | YC-650 | |||||||
Injection Unit | Screw diameter | mm | Φ45 | Φ50 | Φ50 | Φ55 | Φ50 | Φ55 | |||
Shot volume | cm3 | 366 | 451 | 530 | 641 | 471 | 570 | ||||
Shot weight | gram | 338 | 417 | 490 | 592 | 420 | 509 | ||||
ozs | 11.9 | 14.7 | 17.3 | 20.9 | 14.8 | 17.9 | |||||
Injection pressure | kg/cm2 | 2676 | 2167 | 2309 | 1908 | 2764 | 2284 | ||||
Injection Speed | mm/s | 88 | 82 | 82 | |||||||
Injection rate | cm3/sec | 140 | 172 | 162 | 196 | 160 | 194 | ||||
Screw Speed (max) | rpm | 170 | 190 | ||||||||
Clamping Unit | Clamping force | metric tons | 450 | 550 | 650 | ||||||
Clamping stroke | mm | 600 | 620 | 650 | |||||||
Mold thickness | mm | 200-700 | 320-900 | 350-1000 | |||||||
Rotary Table Diameter | mm | 1250 | 1450 | 150 | |||||||
Distance Between Barrel Centers | mm | 550 | 650 | 37 | |||||||
Distance between tie bar | mm | 1100*600 | 1200*715 | 1260*780 | |||||||
Ejector stroke | mm | 140 | 140 | 140 | |||||||
Electrical Equipment | Pump Motor power | kw | 21.2+21.2 | 30+30 | 30+30 | ||||||
Temperature controller | (range)set | 2-(0-400℃)*5 | 2-(0-400℃)*5 | 2-(0-400℃)*5 | |||||||
Heater power | kw | 26 | 26 | 32 | |||||||
Other | Machine dimensions | mm | 7500*2000*2100 | 7850*2250*2200 | 8000*2250*2200 | ||||||
Machine weight | metric tons | 17.6 | 30 | 32 | |||||||
System pressure | kg/cm2 | 140 | 140 | 140 | |||||||
Platen dimensions | ![]() |
![]() |
![]() |
||||||||
Platen dimensions | ![]() |
![]() |
![]() |
||||||||
Platen dimensions | ![]() |
![]() |
![]() |
TECHNICAL PARAMETERS
Project | Unit | YC-850 | YC-1000 | YC-1420 | |||||||
Injection Unit | Screw diameter | mm | Φ55 | Φ70 | Φ55 | Φ70 | Φ44 | Φ70 | Φ90 | ||
Shot volume | cm3 | 665 | 1500 | 665 | 1500 | 665 | 1500 | 2893 | |||
Shot weight | gram | 614 | 1386 | 614 | 1386 | 614 | 1386 | 2673 | |||
ozs | 21.7 | 48.9 | 21.7 | 48.9 | 21.7 | 48.9 | 94.3 | ||||
Injection pressure | kg/cm2 | 2343 | 2210 | 2343 | 2271 | 2343 | 2210 | 1815 | |||
Injection Speed | mm/s | 105 | 105 | 105 | |||||||
Injection rate | cm3/sec | 249 | 403 | 249 | 403 | 249 | 403 | 667 | |||
Screw Speed (max) | rpm | 160 | 180 | 160 | |||||||
Clamping Unit | Clamping force | metric tons | 850 | 1000 | 1420 | ||||||
Clamping stroke | mm | 1000 | 1100 | 1300 | |||||||
Mold thickness | mm | 400-1100 | 700-1300 | 700-1300 | |||||||
Rotary Table Diameter | mm | 1500 | 1600 | 1930 | |||||||
Distance Between Barrel Centers | mm | 700 | 710 | 710 | |||||||
Distance between tie bar | mm | 1060*1060 | 1130*1130 | 1330*1330 | |||||||
Ejector stroke | mm | 140 | 140 | 130 | |||||||
Electrical Equipment | Pump Motor power | kw | 31.4+31.4 | 45+45 | 60+60 | ||||||
Temperature controller | (range)set | 2-(0-400℃)*5 | 2-(0-400℃)*5 | 2-(0-400℃)*5 | |||||||
Heater power | kw | 58 | 58.7 | 67.9 | |||||||
Other | Machine dimensions | mm | 11100*2250*2300 | 11200*2300*2500 | 11500*3050*2750 | ||||||
Machine weight | metric tons | 50 | 56 | 70 | |||||||
System pressure | kg/cm2 | 140 | 140 | 140 | |||||||
Platen dimensions | ![]() |
![]() |
![]() |
||||||||
Platen dimensions | ![]() |
![]() |
![]() |
||||||||
Platen dimensions | ![]() |
![]() |
![]() |
Note: The output of this product parameter is calculated according to the specific gravity of polystyrene of 1.05, assuming an efficiency of 0.88. As the product is continuously researched and improved, the design changes are subject to change without notice.
Next: Two-color injection molding machinePrevious: First page